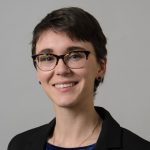
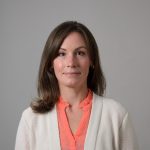
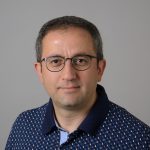
The Institute of Materials Science (IMS) at UConn is pleased to announce the addition of three new staff members who will enhance the Institute’s research and outreach capabilities.
Jesse David joined IMS as Stock Room and Lab Safety Manager in March. Jesse comes to IMS from within the University, having previously served as environmental health and safety coordinator for the Innovation Partnership Building (IPB). An analytical chemist interested in research and development, cannabis, and quality testing roles, Jesse brings a strong background in method validation and analysis on HPLC, UPLC, GC/MS, GC/FID. Jesse holds a B.S. in Chemistry from the University of South Florida and has held positions of increasing responsibility at alternative medicine company Trulieve in Tallahassee, Florida. An avid environmentalist, Jesse has volunteered for environmental agencies including Coastal Cleanup in Tampa Bay, FL, and the Tampa Audubon Society.
Nicole Jagielo joins IMS as the new Grants and Contracts Assistant. Nicole will report directly to Christina Tamburro to support the post-award grant needs of IMS researchers. Nicole has extensive experience with payroll and HuskyBuy processing at UConn, having worked in several departments and centers across the university. She holds a bachelor’s degree from Rutgers University.
Dr. Mustafa Selman Yavuz joins IMS as the new clean room manager. He received his Ph.D. in Chemistry at UConn working with Dr. Greg Sotzing. He completed his postdoctoral work at Washington University with Dr. Younan Xia. Mustafa was formerly the R&D Director of 3BC Inc., a consultant, and Director at Biyotez Kimya Limited. Mustafa will be responsible for running the clean room and training researchers on the proper use of clean room equipment.
IMS is an advanced materials research institution providing superior graduate research education in the interdisciplinary fields of materials science and polymer science and offering materials-related technical outreach to Connecticut’s industries.